D. I. Kryuchkov , A. G. Zalazinsky , I. M. Berezin , O. V. Romanova
MODELLING OF COMPACTION OF TITANIUM COMPOSITE POWDERS
DOI: 10.17804/2410-9908.2015.1.048-060 The quality of finished products is determined at the stage of compaction. High-pressure cold compaction sometimes fails to provide the coalescence of VT-22 high-strength titanium alloy powder particles. Particle coalescence is governed by mechanical characteristics, the spherical particle shape and hard oxide on the particles of the VT-22 powder. This results in the low strength workpieces. To ensure the strength of a compact, powder additives with more plastic properties are used. Simulation is applied to find an optimum additional powder and its volume. The process of compaction is simulated with the use of a representative volume element for a composite made of the VT-22 and PTM-1 powders. The forming and coalescence of particles are represented in uniform triaxial and uniaxial compression. It is shown that the increase in the percentage of VT-22 to more than 50 % in the mixture prevents the uniform spreading of the more ductile component PTM-1. The parameters of the modified Drucker-Prager Cap model are identified for 50/50 and 75/25 VT-22 and PTM-1 powder composites. Compaction in a closed container is simulated. Problems are solved with the application of program packages developed for Abaqus. Experiments on compacting and breaking workpieces made of the pure powders and their two mixtures are made to validate the adequacy of the solution results.
Keywords: powder, titanium, compaction, simulation, coalescence of powder particles. References: 1. Froes F.H., Smugersky J.E. Poweder metallurgy of titanium alloys. The metallurgical society of AIME Publ., 1980. 263 p.
2. Froes F.H., Eylon D., Bomberger H.B. Powder metallurgy of titaniumium alloys – a review. Titanium Technology: Present Status and Future Trends,1985, pp. 49–59.
3. Abkowitz S., Abkowitz S.M., Weihrauch P.F., Wells M.G. Low cost PM manufacture of titanium alloy components for fatique critical application. Proc. The Third International Conference on Powder Metallurgy in Aerospace, Defense, and Demanding Applications, Princeton, NJ, 1993, pp. 241.
4. Moxson V.S., Senkov O.N., Froes F.H. Production and applications of low cost titanium powder products. The International Journal of Powder Metallurgy, 1998, vol. 34 (5), pp. 45–53.
5. Kari S., Berger H., Rodriguez-Ramos R., Gabbert U. Computational evaluation of effective material properties of composites reinforced by randomly distributed spherical particles. Composite Structures, 2007, vol. 77, pp. 223–231.
6. Mesarovic S.D. Micromechanical modelling of the compaction of low density composite powders. Metalurgija – Journal of Metallurgy, 2005, vol. 11 (1), pp. 1–21.
7. Sridhar I., Fleck N.A. Yield behaviour of cold compacted composite powders. Acta materialia, 2000, vol.48, pp. 3341–3352.
8. Kryuchkov D.I., Zalazinsky A.G. Hybrid modelling complex for optimization processes of extrusion of non-uniform materials. Vestnik kompjuternyh i informacionnyh tehnologij, 2013, no. 9, pp. 22–28. (In Russian).
9. Leon L., Mishnaevsky Jr. Automatic voxel-based generation of 3D microstructural FE models and its application to the damage analysis of composites. Materials Science and Engineering, 2005, vol. 407, pp. 11–23.
10. Shen H., Brinson L.C. Finite element modeling of porous titanium. International Journal of Solids and Structures, 2007, vol. 44, pp. 320–335.
11. Kushch V.I., Podoba Ya.O., Shtern M.B. Effect of micro-structure on yield strength of porous solid: A comparative study of two simple cell models. Computational Materials Science, 2008, vol. 42, pp.113–121.
12. Ogbonna N., Fleck N.A. Compaction of an array of spherical particles. Acta Metallurgica et Materialia, 1995, vol.43, pp. 603–620.
13. Berezin I.M., Zalazinskiy A.G. Identification of the determinative correlations of plastically compressed materials. Fundamentalnye issledovanija, 2013, no. 8, pp. 19–23. (In Russian).
14. Johnson G.R, Cook W.H. Fracture Characteristics of Three Metals Subjected to Various Strains, Strain Rates, Temperatures and Pressures. Eng. Fract. Mech, 1985, vol. 21, pp. 31–48.
15. Bogatov A.A. Mekhanicheskie svoistva i modeli razrucheniya metallov [Mechanical properties and models of fracture of metals]. Ekaterinburg, GOU VPO UGTU-UPI Publ., 2002, 329 p. (In Russian).
16. Semenov A.P. Skhvatyvanie metallov [Adhesion of metals]. Moscow, Mashgiz Publ., 1958, 280 p. (In Russian).
17. Kolmogorov V.L. Mekhanika obrabotki metallov davleniem [Mechanics of metal forming]. Ekaterinburg, UGTU-UPI Publ., 2001, 836 p. (In Russian).
18. Kolmykov V.L., Glazunova M.Ju., Zalazinsky A.G. Drawing a thin wire made of titanium for suture materials. Izvestija VUZov. Cvetnaja metallurgija, 2002, no. 3, pp. 66–69. (In Russian).
19. Kolmykov V.L., Zalazinsky A.G. Deposition of oxide coatings for wire drawing of difficultto-deform materials. Uprochnjajushhie tehnologii i pokrytija, 2007, no. 6, pp. 15–18. (In Russian).
Article reference
Modelling of Compaction of Titanium Composite Powders / D. I. Kryuchkov, A. G. Zalazinsky, I. M. Berezin, O. V. Romanova // Diagnostics, Resource and Mechanics of materials and structures. -
2015. - Iss. 1. - P. 48-60. - DOI: 10.17804/2410-9908.2015.1.048-060. -
URL: http://eng.dream-journal.org/issues/2015-1/2015-1_4.html (accessed: 08/30/2025).
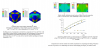
|